Talking To The Source: Dr. Jennifer Russell of Virginia Tech and the Circular Economy
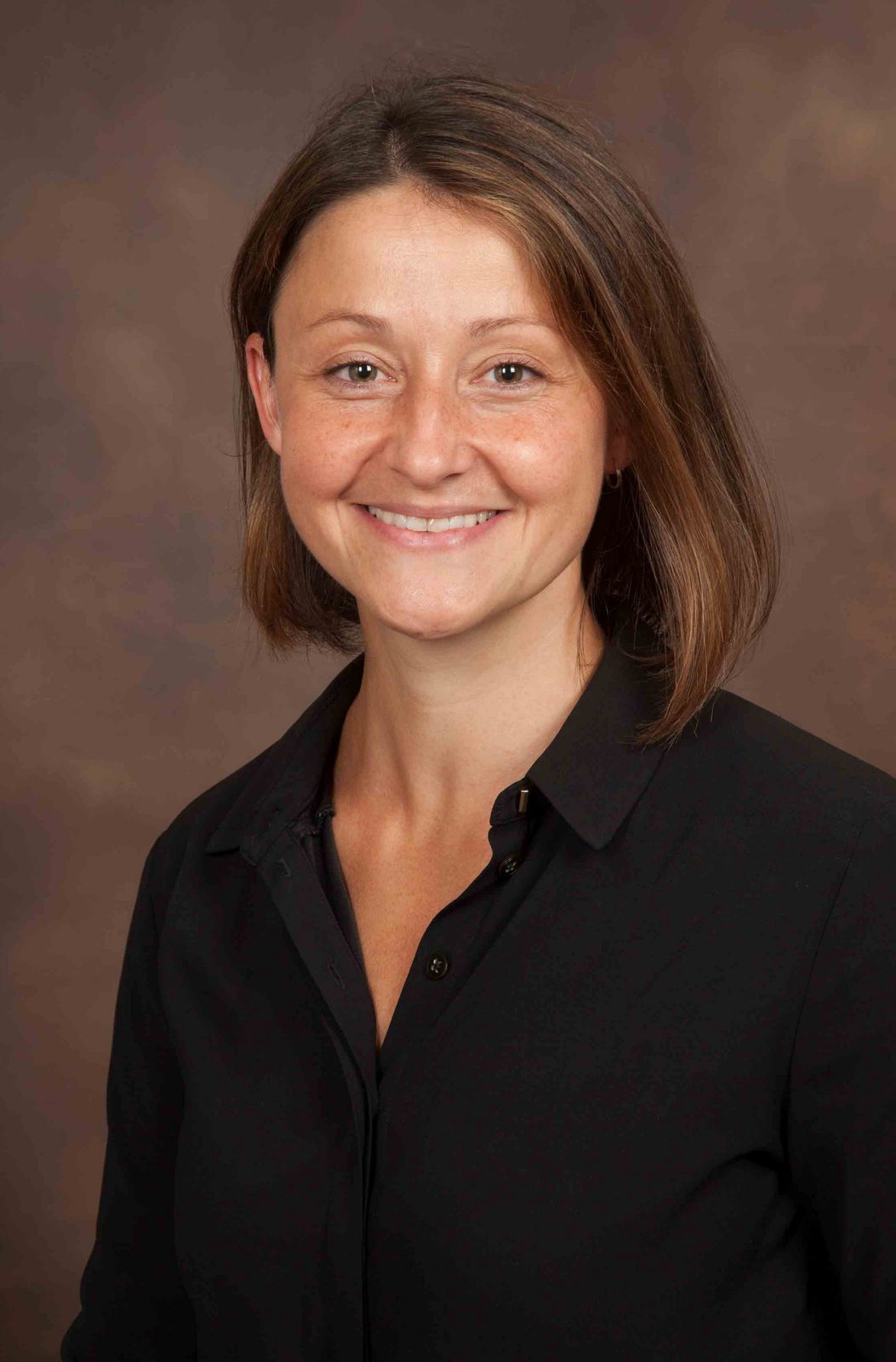
*Editor’s Note: The viewpoint and statements of the following post may not reflect the views of Nature’s Packaging, however, we are always committed to providing an open forum for all members of the forest and forest products community.
Dr Russell, what is your role at Virginia Tech, and what is your area of expertise?
I am an Assistant Professor in the Department of Sustainable Biomaterials, at the College of Natural Resources and Environment. My area of expertise is in economic systems-modeling, with a focus on the environmental impacts associated with industrial use of resources and energy.
Our conventional economic system generates a significant amount of solid waste, consumes a significant amount of fuel and energy, and distributes a lot of pollutants into the water and atmosphere. This system becomes even more problematic when we consider that every product requires materials that must be extracted from the earth and that are destined to go to a landfill when the user is finished with it.
Given all of this, I study how we can incorporate innovative changes into business models and material flows in order to achieve a system that is more ‘circular’ — in which flows of waste materials and products can be integrated as inputs into new production and manufacturing. This effectively reduces the loss of valuable materials into landfills, and it offsets some of the need to extract new materials and resources for inputs to production.
Throughout this system, there are opportunities for reduced energy consumption, reduced emissions, and even increased employment opportunities. This alternative economic framework is called “Circular Economy”, and it is a concept that governments and businesses around the world are engaging with and adopting, increasingly, over the past 10 years.
What is your current area of research in the topic of the “circular economy”?
I am very interested in contributing to the realization and operationalization of circular economy practices and processes – in other words, how are we making these changes now, given the legacy systems, infrastructure, and cultures that exist (and that might pose challenges).
Much of the research in circular economy is focused on high-tech innovation and industrial solutions – these are very important; but also important are the activities, processes, and behaviors that are accessible to everyone around the world.
For this reason, a lot of my current research is focused on the challenges and opportunities related to the increased practice of repair and reuse. Arguably, anyone in the world can engage in these practices, and there are not really many stringent barriers to people participating in repair or reuse.
These processes have also been common-practice for many communities for centuries – they are not ‘new’; However, the ways in which we value these activities, as a society, has changed. Where, a century ago the mending and repairing of goods and equipment was common practice and expected, many categories of goods and equipment have become ‘disposable’; there is a lot of evidence of the decline of the independent repair community, and the relegation of reuse to something only done for charitable purposes.
Other ways I am exploring this theme of ‘operationalizing circular economy’ is through the lens of local policy solutions – how are community leaders and municipal governments engaging with the ideas of circular economy to move it forward in ways that respect local conditions and priorities.
You recently co-authored a UN report, “Re-defining Value – The Manufacturing Revolution”. Why is re-thinking how we manufacture industrial products and deal with them at the end of their useful life so important?
Industry’s singular pursuit of ‘efficiency’ has led to some major environmental and economic challenges. Not only do we have millions of tons of valuable materials being sent to landfill each year because, as a society, we have become normalized to the idea that things can just be ‘thrown’ away; we are also facing a realization that many of the resources and materials that we have relied on for the past 100 years are finite, and that we might actually run out of them.
Although the word “sustainability” is now used in a variety of ways, fundamentally, industry decision-makers are starting to think about the longevity, security, and resiliency of their supply chains – our ability to ‘sustain’, ourselves, our economies, our health, our way of life, and the future of our children.
The analogy of a “linear economy” really highlights this challenge: We take materials from the ground; we convert them into products; we use those products; and then we throw them away – a figurative “take–>make–>dispose” system. When we manufacture products in a linear system we also generate other negative environmental impacts associated with production: for every new product made, energy and fuel are consumed, solid waste and pollutants are generated, and emissions are released into the atmosphere.
Unlike nature, a linear economy does not replenish stores of valuable materials, and it does not return any nutrients back into the environment; it depletes resources in one place, and concentrates wastes and valuable materials alike into inaccessible landfills. It is easy to see that this model is really not sustainable at all.
The idea of cycling materials, components, and products within a circular economy is really about mimicking nature: In a forest there is no waste – every item within that ecosystem is part of an elaborate food web that includes plants, bacteria, herbivores, omnivores, and carnivores. The solution to our challenge of finite materials and environmental damage is to find the industrial analogy of a food web: In other words, how can we organize and manage material and product flows so that there is no waste, and so that we do not run out of the materials we need to keep our economies running?
Goals to achieve zero-waste to landfill can be helpful, because they focus on finding valuable applications and outlets for materials and products that are no longer wanted by the original owner. However, we cannot rely on recycling alone: Only a small subset of products and materials can be recycled; many products have components and materials that are so integrated, that we cannot separate them out to be recycled (e.g. old laptops and smart phones); and recycling processes can require a lot of energy. Further, many of the products entering the waste stream are still functional and have a lot of residual value.
Many of these waste stream challenges can be addressed much further upstream in the process, through improved design and manufacturing practices: designing products to be easily disassembled, easily repaired, modular, and/or upgradable are key ways that we can enable a product to have multiple long service lives.
Manufacturing products and reorienting business models in a manner that allows for the use of recaptured parts, instead of new parts, can significantly reduce the amount of new materials that are required for production, as well as the associated cost, energy, and time.
Join us next week on the Nature’s Packaging Blog for Part 2 of this interview.